Sustainability Series – Part 6 – Warehousing
In the first parts of this Sustainability Series, we have considered the pressures the transport sector is facing globally to reduce greenhouse gas emissions in light of the global climate crisis. However, changes need to be made across the supply chain in order to effect a profound difference.
The e-commerce industry has been growing exponentially for a number of years with more than one quarter of UK retail sales now generated by e-commerce. 1 Notably, UK warehousing stock increased by 138 million square foot and 444 units between 2015 and 2021. Such growth was accelerated by the pandemic and strict government lockdown measures in 2020 and 2021 which drove consumers to shop online. Although post-pandemic the e-commerce sales market saw a small decline, e-commerce is expected to represent 38.1% of all retail sales in the UK by 20252. As a result, there is an increasing need for additional warehousing space.
According to the World Green Building Council, buildings are responsible for 39% of global energy related carbon emissions 3. 11% of such emissions are due to embodied carbon i.e., the emissions associated with the materials and construction process throughout the lifecycle of a building or infrastructure and 28% are attributable to operational carbon (the amount of carbon emitted during the building’s operations i.e., the carbon emitted keeping the building warm, cool, powered, light etc.)4. Currently, in order to achieve a high Building Research Establishment Environmental Assessment Method (BREAAM) rating, buildings tend to have a 50/50 split between embodied carbon and operational carbon. However, in many existing warehouses, operational carbon makes up around 70% of the aggregate5. With demand for warehousing space increasing, the need to take a low-carbon approach to construction and building maintenance as well as reducing emissions associated with operations is pivotal for reducing carbon in this sector of the logistics industry.
Interestingly, there are already a handful of international major brands, such as L’Oréal and Nike paving the way to more sustainable warehousing practices and which operate carbon neutral warehouses that have been custom-built with specialised infrastructure to reduce the amount of steel and concrete used in construction, and which are run purely on renewable energy6. Earlier this year, Prologis, the UK’s leading developer and owner of logistics parks also completed the construction of the UK’s first property to go beyond net-zero carbon in its construction and operation (including rainwater harvesting and electric vehicle charging infrastructure and a 1.4MW rooftop solar system which will mean the building will return more energy to the gird than it uses, with surplus energy generated being used to help power other homes and businesses)7. However, more organisations must follow suit in order for the UK government to reach its goal of net zero emissions by 2050.
Legal/Regulatory Incentives
Changes in policies, regulations and economics have pushed logistics providers to meet more stringent carbon emissions requirements. The UK Government’s Energy White Paper, published in December 2020, stated that by 2030, all non-domestic buildings must achieve an energy performance certificate ( EPC) (which provides a measure of energy efficiency and CO2 emissions) rating of B and a minimum EPC rating of C by 20278. Further, from 2023, landlords will be prevented from continuing to let F and G rated structures9. As, currently, around 60% of commercial buildings still have no EPC and of those that do, around 18% are F or G rated with a further 22% being E rated10, there is clearly a substantial amount of work to be done by owners and lessees of warehouses to meet emissions regulations.
However, as part of the UK’s efforts to meet its zero emissions targets, in April 2022, the Government published the national energy security strategy which included a proposal to increase solar deployment by 2035 11. Crucially, the use of solar panels in the UK’s warehousing industry offers huge potential to both increase efficiency and reduce emissions.
Solutions/Alternative Options
Decreasing demand for electricity
Whilst solar panels have been around for around 140 years, their uptake has been relatively slow. The advantages of solar panels are well known but the associated costs and weather dependency has led to many industries opting for alternative measures. In a recent report by the United Kingdom Warehousing Association ( UKWA) and Delta Energy & Environment (Delta-EE) it was found that the installation of solar panels on the roofs of warehouses could provide the UK with double its current solar capacity and result in a reduction of carbon emissions by 2 million tonnes a year12. Currently, warehouse roofs account for nearly a third of all commercial roof space in the UK13, and so provide enormous potential for carbon reduction methods.
As electricity prices have doubled since 2021, and are predicted to continue to rise in 2023, the potential of solar panels to reduce annual electricity costs by 40 to 80% is significant.
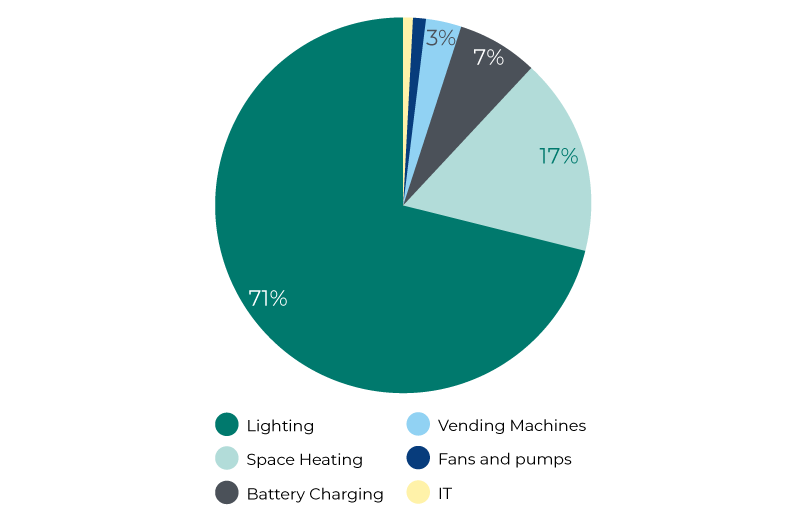
Figure 1 – Energy usage breakdown for an average 15,000m2 warehouse (with no refrigeration)14.
Installing solar panels allows warehouses to create their own energy source and to use this energy to power their own operations. There is also the chance to sell excess energy back to the national grid or to local communities. This will additionally help reduce warehouses’ exposure to price fluctuations in the energy market.
Reducing waste
Although the logistics and warehousing sectors have the highest proportion of automation of any industry, in order to meet the increasingly high levels of e-commerce demand it is likely that the rate of automation will rapidly increase in the next 5 to 10 years. Whilst automation is usually introduced as a way of offsetting labour shortages instead of as a way of meeting environmental issues, automation has the potential to reduce energy usage and increase efficiency in warehouses. Automation comes in a variety of different forms from bar-coding and radio frequency identification ( RFID) to implementing a Warehouse Management System (WMS) and an automated storage and retrieval system (ASRS).
For companies implementing bar-coding and RFID, the need for paper will dramatically reduce as systems are digitalised, creating savings and reducing warehouses’ environmental footprint. A WMS can assist warehouse operation efficiency and productivity whilst improving asset and space utilisation. Space optimisation and ensuring the physical space of warehouses is being used efficiently, will reduce the need for additional warehouse developments, therefore not only saving costs but also reducing waste. A major issue in the logistics industry relates to the ability to trace and locate products and implementing an automated system can provide greater visibility of products thereby decreasing the risk of resources and energy being wasted. An ASRS can additionally assist warehouse operators with more effective sorting and retrieval. It offers creative storage solutions which can reduce a warehouse’s physical and environmental footprint, for example, looking at how vertical space is used in warehouses. Reusing as many materials as possible, avoiding single-use plastics and recycling waste materials will also assist in making warehouses more sustainable.
As shown in Figure 1, lighting is a key contributor to the amount of energy consumed by warehouses. However, switching sodium or metal halide discharge lighting to light-emitting diodes ( LEDs) has the potential to reduce electricity usage by 50%. LEDs’ operating lifetime is also significantly longer than traditional light bulbs which can provide cost savings over time15.
Essentially, increasing the use of automated systems and implementing small changes such as switching to LEDs or energy-efficient material handling equipment can improve warehouse productivity and efficiency, therefore reducing waste and energy usage.
Building warehouses sustainably
As mentioned above, in order to make warehouses as efficient and sustainable as possible, efforts need to start with the construction process. However, whilst construction companies are focusing on building warehouses using sustainable and recycled/recyclable materials, offsetting remains and will continue to remain key. Offsetting is usually carried out through reforestation, renewable energy or energy conservation projects. For example, Prologis offsets unavoidable embodied carbon emissions by protecting 310 acres of Papua New Guinea’s rainforest. Whilst carbon offsetting can be beneficial, its susceptibility to allegations of varying degrees of greenwashing can, in some cases, negate its impact and as such, caution should be taken when engaging in carbon offsetting programmes. 16
Barriers to change
As we have explored so far, implementing changes to achieve net zero and reduce emissions can also assist to reduce overall waste and increase efficiency and productivity. However, solutions can require vast amounts of capital, time, compliance with burdensome laws and regulations and the appetite of the market and stakeholders alike.
The economics associated with implementing solar panels are often influenced by the upfront costs of installation and the extent self-consumption is viable. The upfront cost of installing solar panels often equates to 70-80% of the aggregate project costs. However, due to the seasonal and temporal nature of solar power, it is often difficult for businesses to match supply and demand. For example, there is usually higher demand for energy in the winter months, but due to the weather, solar energy generation is usually unable to meet this demand. Conversely, in the summer, energy generation is a lot higher than demand. 17
In terms of contractual issues, there mut be a clear understanding between the tenant, landlord and any other relevant parties that allows for the installation of new systems, machinery or infrastructure. Planning permission and permits are also often required and can increase the length of time needed to implement solutions. Ultimately, a clear understanding of the energy requirements of warehouses is crucial to employing appropriate measures. Construction firms and warehouse operators must be aware of the costs associated with maintaining a warehouse throughout its operational life and also those associated with the decommissioning, dismantling and recycling of materials used in the construction of a warehouse at the end of its life 18. There may also be a disconnect between what the warehouse can achieve in terms of sustainability and how much the local infrastructure can support.
Timing is also an issue, as where some solutions tend to be long term investment projects which require between 10 and 15 years, lease durations may be shorter which often means there is not sufficient time to realise financial benefit. The opportunity to realise investments additionally diminishes over the duration of a lease. The discord between longer term sustainability projects and lease durations together with the expansion of the role of third-party logistic models (which require agile operations to manage short term customer contract risks and short leases) accentuates this problem 19.
Conclusion
The efforts of the UK Government and international community to achieve net-zero by 2050 has pushed sustainable practices to the forefront of stakeholders’ priorities in the logistics and warehousing sectors. However, the high costs associated with the implementation of sustainable practices and the disconnect between the duration of typical commercial leases and the time needed to realise green investments has reduced the speed at which such practices are being established. That being said, tightening legislation in respect of commercial buildings’ environmental impact will continue to incentivise warehouse operators to implement sustainable practices and solutions.
Whilst the cost of investing in sustainable warehousing is inevitably high, it is paramount to enforce worthwhile change and assist in the fight against climate change.
How HFW can help
HFW has a wealth of experience in the transport and logistics sector and can work with clients to achieve their sustainability goals by providing solutions for both sustainable transport and logistics and the entire life cycle of the supply chain.
Footnotes
- Statista. E-commerce share of retail sales revenue in the United Kingdom (UK) from 2020 to 2025. Available at: E-commerce share of UK retail sales 2020-2025 | Statista
- Statista. E-commerce share of retail sales revenue in the United Kingdom (UK) from 2020 to 2025. Available at: E-commerce share of UK retail sales 2020-2025 | Statista
- World Green Building Council. Bringing embodied carbon upfront. Available at: Embodied Carbon – World Green Building Council (worldgbc.org)
- World Green Building Council. Bringing embodied carbon upfront. Available at: Embodied Carbon – World Green Building Council (worldgbc.org)
- SHD Logistics. A sustainable future for warehousing. Available at: A sustainable future for warehousing (shdlogistics.com)
- Supply Management. Nike opens warehouse running on 100% renewable energy. Available at: Nike opens warehouse running on 100% renewable energy – Supply Management (cips.org)
- SHD Logistics. Prologis completes first beyond net-zero warehouse project. Available at: Beyond net-zero warehouse project completed by Prologis (shdlogistics.com)
- Energy White Paper. Powering our Net Zero Future. Available at: Energy White Paper (publishing.service.gov.uk)
- sbh. New Energy Building Standards for Warehouses. Available at: New energy building standards for warehouses | sbh
- sbh. New Energy Building Standards for Warehouses. Available at: New energy building standards for warehouses | sbh
- HM Government. British Energy Security Strategy – Secure, clean and affordable British energy for the long term. Available at: British Energy Security Strategy (publishing.service.gov.uk)
- Supply Management. How the UK warehousing sector can be used to boost solar energy. Available at: How the UK warehousing sector can be used to boost solar energy – Supply Management (cips.org)
- Supply Management. How the UK warehousing sector can be used to boost solar energy. Available at: How the UK warehousing sector can be used to boost solar energy – Supply Management (cips.org)
- Carbon Trust. Warehousing and logistics – Energy efficiency opportunities for warehousing and logistics companies. Available at: Warehousing-and-logistics-guide.pdf (windows.net)
- ENWL. Measures to reduce CO2 emissions for warehouses and factories. Available at: measures-to-reduce-emissions-manufacturing-and-warehouses.pdf (enwl.co.uk)
- Earth.Org. Is Carbon Offset a Form of Greenwashing? Available at: Is Carbon Offset a Form of Greenwashing? | Earth.Org
- UKWA. Investment case for rooftop solar power in warehousing. Available at: Delta-EE Publications (ukwa.org.uk)
- UKWA. Investment case for rooftop solar power in warehousing. Available at: Delta-EE Publications (ukwa.org.uk)
- UKWA. Investment case for rooftop solar power in warehousing. Available at: Delta-EE Publications (ukwa.org.uk)
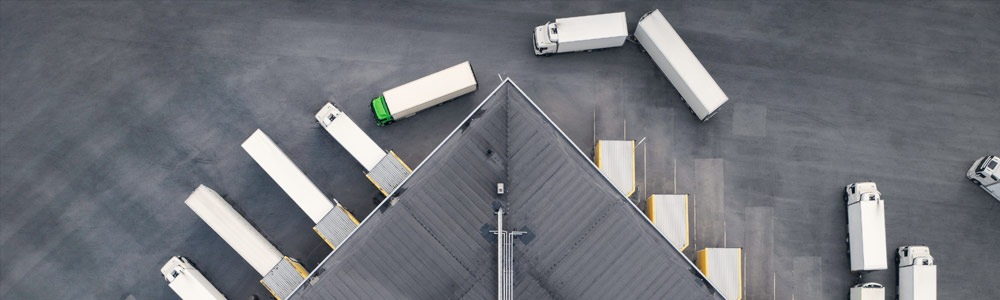